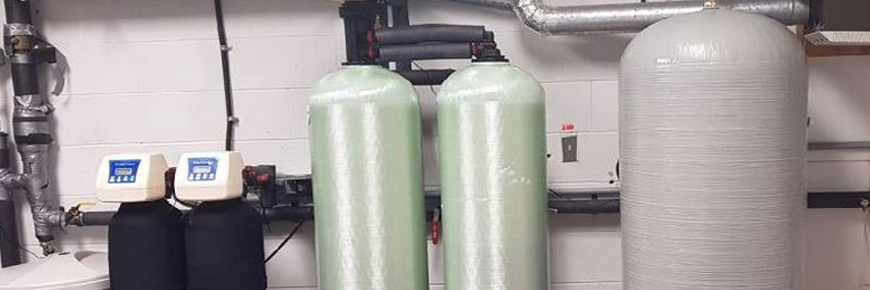
Potable water transformation
Pukaskwa National Park
by Katie Zugic
Pukaskwa National Park hosts over 10,000 visitors annually, which necessitates a water system that ensures economic, social, and environmental goals are met. When the old water system required $50,000 of maintenance and complex training requirements, the Assets team at Pukaskwa came up with a more efficient and sustainable method to meet the needs of visitors camping at the park.
Pukaskwa National Park previously employed one large, centralized water filtration system to supply treated water to the comfort stations and potable water sources in the campground, and a well-fed microsystem to feed the administration building. The centralized system would intake water from Hattie Cove, run it through a series of filters, inject chlorine for residual, then pool it in large holding tanks until dispersal was necessary. This system required a series of elaborate filters and a Level 2 Water Operator certificate to perform the maintenance necessary to maintain the system, and had $50,000 of deferred maintenance necessary to complete for the upcoming season. This posed a challenge for Park employees as obtaining this certificate is no easy feat, taking up to 2 years working under a licensed operator.
The implementation of the new potable water system cost a fraction of the price of the deferred maintenance of the previous system, and employs four smaller microsystems. The new system employs point of use filtration methods, digital infrastructure, and less stringent testing requirements—making it much simpler to work on. The new system also boasts a lower operational cost, with anticipated yearly maintenance around $400 per microsystem, whereas the old system required around $5000 a year.
Transitioning from a centralized system to microsystems changes the testing requirements for the water system; instead of daily testing for turbidity the staff only need to test twice per week. When you’re as busy as the Assets crew at Pukaskwa a little extra time makes a huge difference. The simplicity of the new filtration system has enabled the park to offer maintenance training to multiple employees which can be completed over the course of 7.5 hours. This allows for a great deal of flexibility regarding maintenance; if one employee is sick or away, the park will not run the risk of losing all expertise.
Having identical systems allows for a higher standard of maintenance to be implemented and identical parts to be used, which decreases the complexity associated with procuring the parts to maintain the system. This makes life much easier for staff and reduces maintenance costs.
The new system boasts impressive measures of sustainability, using a fraction of the water that the old system required. This can be attributed in part to separating the supply piping in the comfort stations. Instead of all fixtures being fed with potable water the toilets and urinals are fed with raw untreated water while the showers, sinks, and hose bibs will be served by the new micro system. With the separation of the supply piping the park is now producing approx. 2700 litres a day less of treated water in the campground, greatly extending the life of the filters and decreasing wear on the system. The new system also requires smaller filters meaning there is less waste, and less wastewater overall. Each system took around one week to install, but the entire process required four months of planning and preparation.
<< Back to shoreLINES
- Date modified :